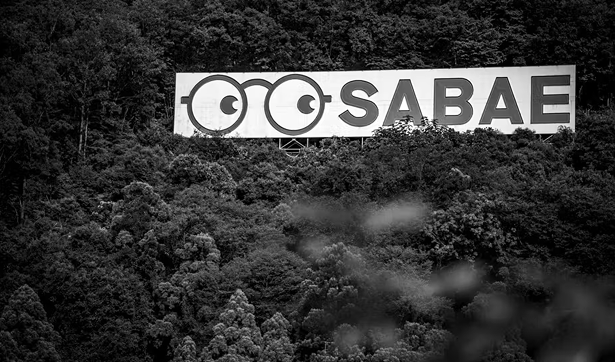
Each limited-edition Jacques Marie Mage spectacle has a story, one told through a design language that references cultural icons and artistic movements from modern history.
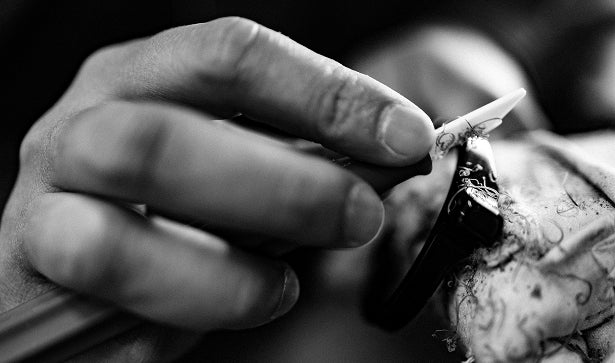
Handcrafted in Japan using a combination of traditional methods and innovative techniques, each pair of glasses requires a 300-step process enriched by the expertise of nearly 100 artisans over 18 months.
Skilled Artisans
With over 300 steps in the production process, we rely on and wholeheartedly respect the artisans that work on our behalf, and support the efforts of our production partners in supporting ethical production methods and providing fair trade wages and benefits.
Acetate
To create frames of incomparable quality, we utilize the finest cellulose acetate: a renewable, non-petroleum, plant-based material that is durable, attractive, and hypoallergenic.
Titanium
Taking nearly 5 months to create a single pair, our Titanium Series glasses are durable, lightweight, and sophisticated spectacles that serve as a proper testament to artisanship and ingenuity.
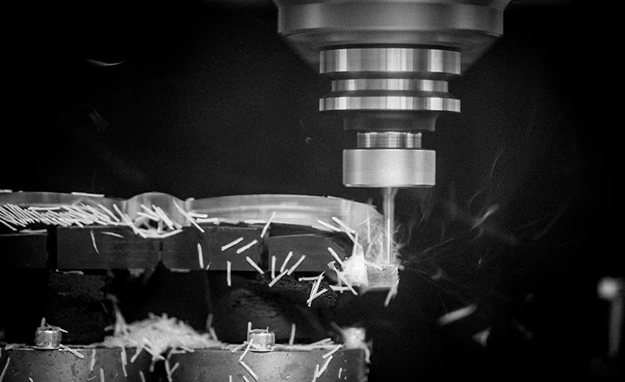
Using state-of-the-art machinery, frame fronts and temples are cut from 10 mm cellulose acetate blocks.
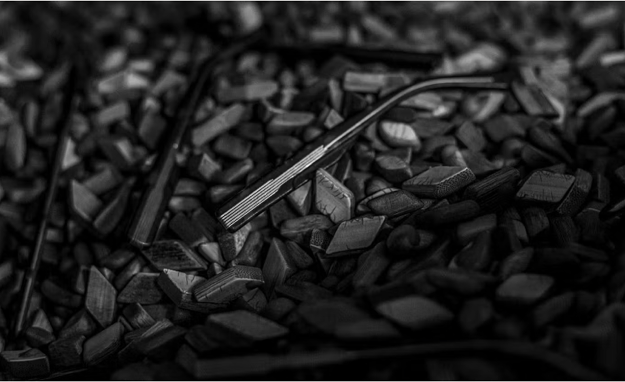
Frame fronts and temples are tumbled in barrels of custom bamboo wood chips to create a smooth and shiny finish.
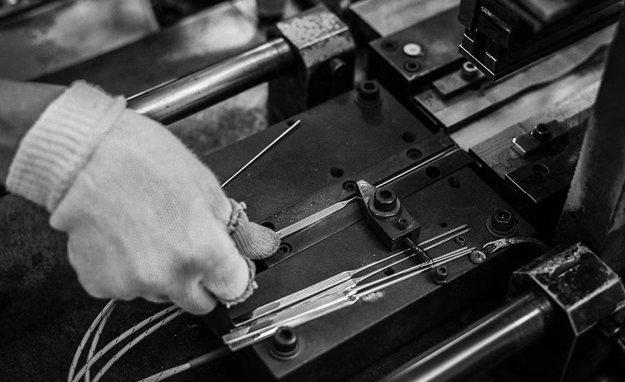
Custom-tooled wirecores are injected into temples to strengthen and stabilize the frame.
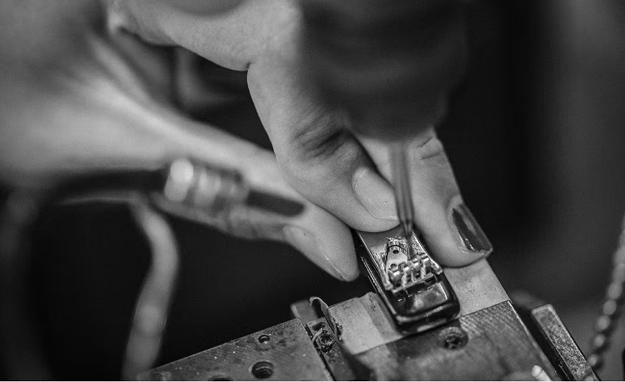
Arrow-shaped hinges mount temple to frame with tension secured pins that ensure optimal calibration.
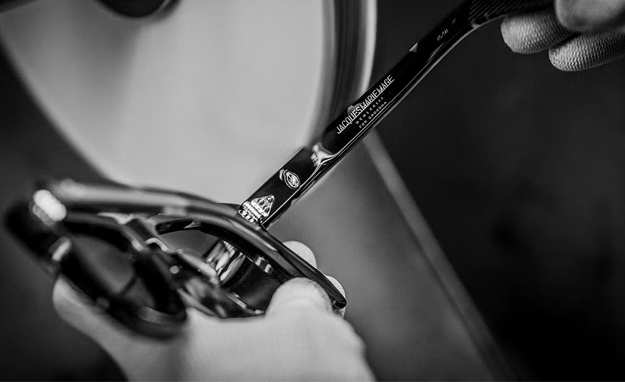
The hand-polishing process requires as many as 10 additional steps to give the frames their signature brilliance.
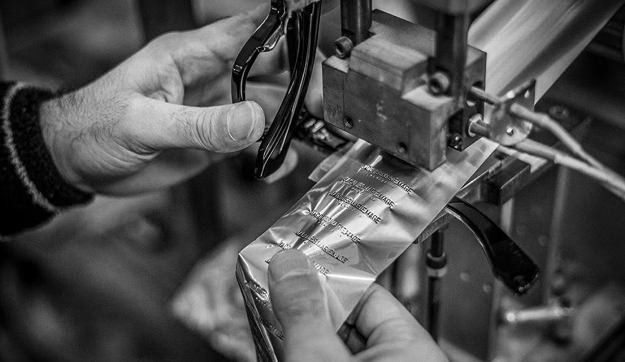
The interior of each Circa Collection frame is marked using a hand-machined foiling process, of either gold or silver leaf, which embeds the metallic color into our acetate temples.
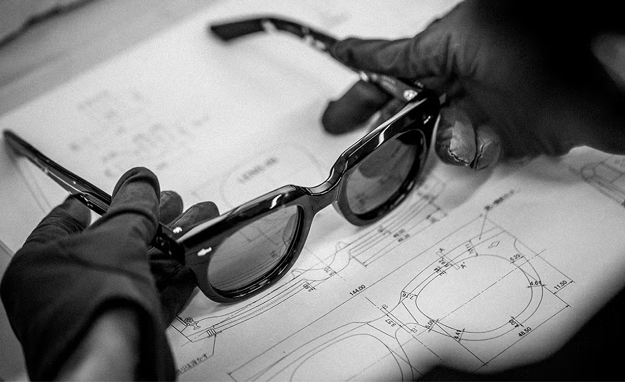
A twenty-point measurement test for all fit specifications and detail finishes virtually eliminates any chance of production flaws.
Acetate
Cutting
Tumbling
Injection
Mounting
Polishing
Foiling
Assuring
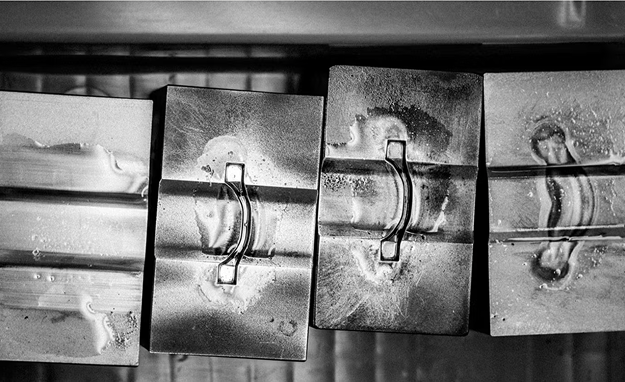
The process starts with building molds out of high carbon die steel with a 10-micron tolerance, which is 10 times more accurate than an acetate tool.
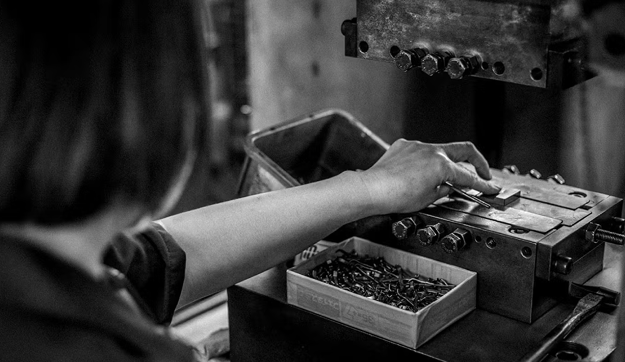
Frame parts are forged by Japanese metal presses, often using as much as 350 tons of pressure to bend and mold the titanium into precise mechanical parts.
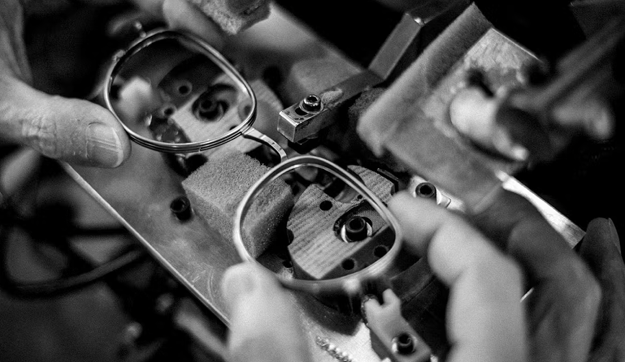
Artisans weld sections of the frame in bursts lasting 0.5 seconds, making sure to moderate pressure, temperature, and electric current. Smaller parts of the frame are laser welded to ensure flawless construction.
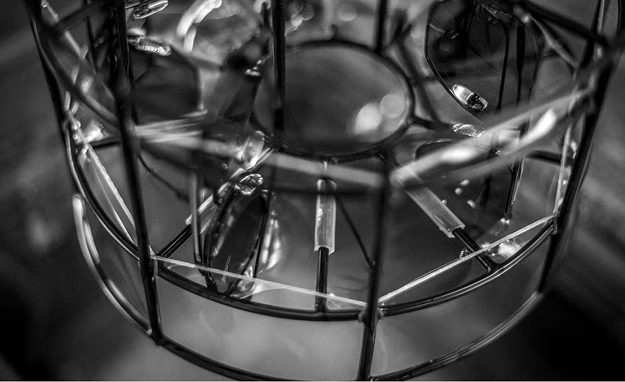
Parts are cleaned using ultrasonic purified water, eliminating any trace of oil or grease to ensure absolute perfect welding.
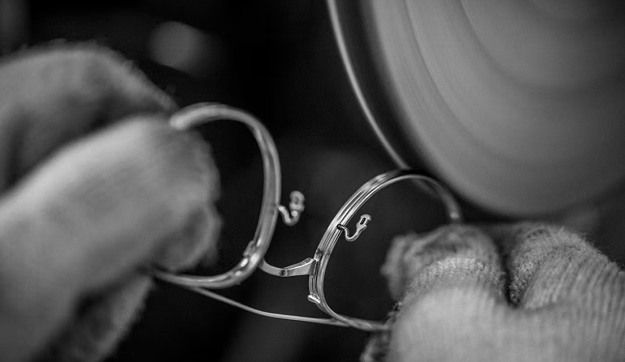
Each frame is polished by hand over 5 times to ensure the perfect finish. The art of polishing is one that takes decades to master, and it is this important step that reveals the full beauty of the titanium frame.
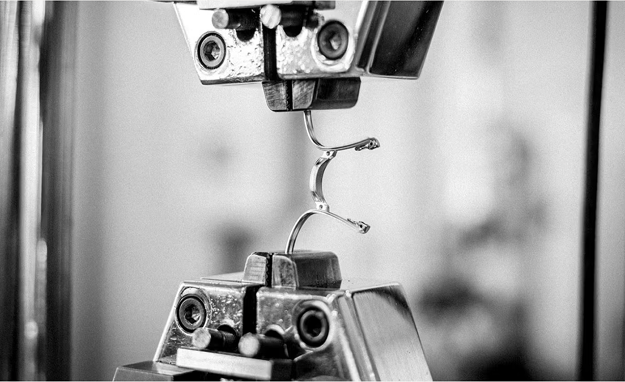
Applying force and elongation techniques to test for stress and fatigue in order to ensure optimal tensile strength.
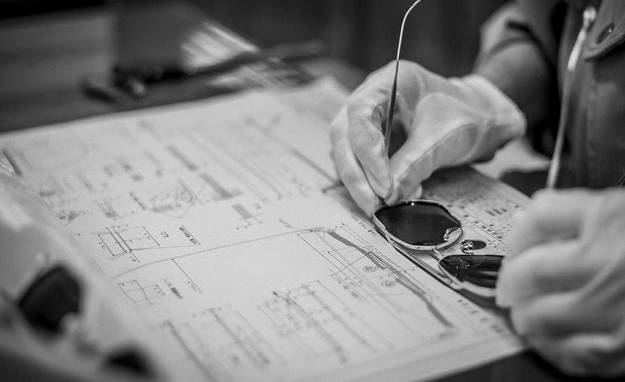
A twenty-point measurement test for all fit specifications and detail finishes virtually eliminates any chance of production flaws.